沖壓工藝的缺點有哪些

沖壓工藝是一種常用的金屬加工方法,但它也存在缺點。沖壓工藝需要使用模具來進(jìn)行成形,一旦需要生產(chǎn)新的產(chǎn)品,就需要制造新的模具,這會增加生產(chǎn)成本和時間。沖壓工藝對材料要求較高,一旦材料的強(qiáng)度和韌性不符合要求,就會導(dǎo)致成形難度增加和產(chǎn)品質(zhì)量下降。沖壓過程中產(chǎn)生的沖擊力和振動會使模具磨損加劇,導(dǎo)致模具壽命減少,增加了維修和更換的成本。沖壓工藝對產(chǎn)品的形狀和尺寸有一定限制,無法處理過于復(fù)雜或超大尺寸的零件。在選擇加工方法時,需要綜合考慮沖壓工藝的優(yōu)勢和缺點。
1、成本高
沖壓工藝是一種常用的金屬加工方法,它的應(yīng)用廣泛,但也存在著缺點。其中之一就是成本高。沖壓工藝的高成本主要體現(xiàn)在兩個方面。
沖壓工藝需要使用大型機(jī)械設(shè)備,這些設(shè)備的購買、維護(hù)和運(yùn)營成本都非常昂貴。特別是在沖壓件的生產(chǎn)規(guī)模較小的情況下,設(shè)備的利用率較低,導(dǎo)致單位產(chǎn)品的生產(chǎn)成本相對較高。
沖壓工藝模具的需求非常高。模具是沖壓過程中最重要的工具,其制作和維護(hù)的成本非常高昂。特別是形狀復(fù)雜、精度要求高的沖壓件模具的制作和調(diào)試成本更是很高。
沖壓工藝存在著其他的缺點,工藝適用性較差,材料的選擇有一定的限制,且沖壓過程中易產(chǎn)生應(yīng)力集中、變形和變色等問題。
沖壓工藝的成本高是其缺點之一。沖壓工藝的應(yīng)用需要在成本和產(chǎn)品質(zhì)量之間做出權(quán)衡,以確保經(jīng)濟(jì)效益和市場競爭力的平衡。也需要不斷改進(jìn)沖壓工藝,降低成本,提高效率,以滿足市場需求。
2、準(zhǔn)確性不高
沖壓工藝是一種常用的金屬加工方法,有很多優(yōu)點,但也存在缺點。沖壓工藝的準(zhǔn)確性不高。金屬材料的彈性變形和模具的磨損等因素,沖壓件的尺寸和形狀會有一定的偏差。沖壓工藝對材料的適應(yīng)性較差。不同材料的脆性、可塑性等性質(zhì)不同,某些材料沖壓會導(dǎo)致裂紋、變形等問題。沖壓工藝的生產(chǎn)效率相對較低,尤其是復(fù)雜形狀的零件需要設(shè)計和制造更復(fù)雜的模具,增加了生產(chǎn)成本和周期。沖壓工藝特殊形狀的零件難以實現(xiàn),需要采用其他加工方法。沖壓工藝有很多優(yōu)點,但準(zhǔn)確性不高是它的一個缺點。在應(yīng)用沖壓工藝時需要綜合考慮其優(yōu)缺點,選擇合適的加工方法。
3、制造周期長
沖壓工藝在制造過程中存在制造周期長的缺點。沖壓工藝需要進(jìn)行多道工序,包括模具制作、材料切割、沖壓成形等,每一道工序都需要時間來完成。沖壓工藝復(fù)雜形狀的零件加工,需要設(shè)計和制造更復(fù)雜的模具,這也會增加制造周期。沖壓工藝進(jìn)行產(chǎn)品的裝配和調(diào)試,以確保產(chǎn)品的質(zhì)量和性能,這些步驟也會延長制造周期。在沖壓工藝中,制造周期的長短與零件的復(fù)雜程度、模具的制造周期裝配調(diào)試的時間密切相關(guān)。為了縮短制造周期,優(yōu)化模具制造工藝、提高沖壓設(shè)備的效率,加強(qiáng)產(chǎn)品的設(shè)計和裝配能力,以降低制造周期,提高生產(chǎn)效率。
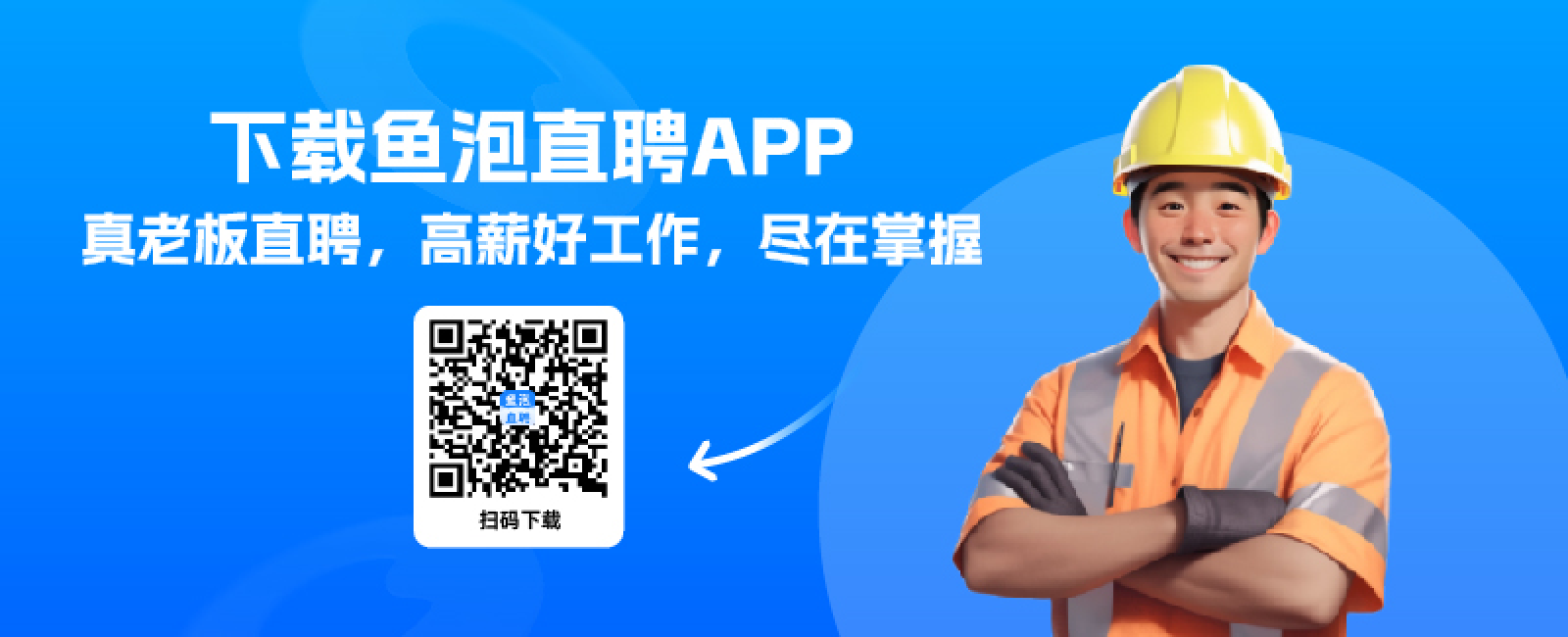





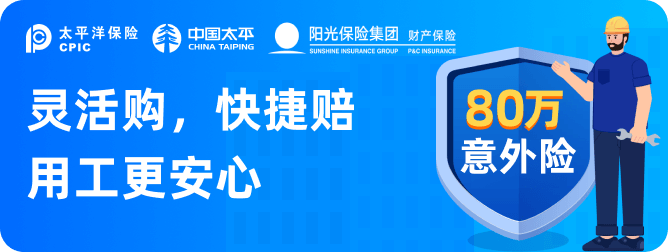